Steel can help prevent your business from going up in flames
Steel and fire-rated glazed glass are part of the essential front-line barrier to prevent and contain accidental fires at your industrial or manufacturing business.
“The finest steel has to go through the hottest fire”. What is born in the blast furnace is also what makes it more resistant to fire in its later life. Steel construction offers clear advantages over other building materials, especially wood. It’s exceedingly strong despite its low weight, it can be formed into whatever shape is necessary for elaborate architectural features and designs, it looks sophisticated and modern and it is very affordable to produce. Using steel in your construction helps keep overall construction costs down.
What is sometimes overlooked is steel’s importance to preventing and limiting damage caused by fire. Unlike other construction materials like timber, metals absorb heat rather than combusting, allowing them to become an important barrier in preventing the spread of fire.
Steel is the fire-rated choice building material for good reason
We tend to think of the purpose of buildings in their best of times – how it is going to be used every day. But business is unpredictable. And in industrial uses with heavy machinery, chemicals, inventories of combustible material and high manufacturing temperatures, the risk of fire becomes a huge concern. It’s the most critical reason why incorporating steel construction into warehousing and industrial facilities has become essential. Steel is strong, protective and resistant to fire.
Steel is a standard fire-rated choice for both structural framing and for walls and roofs (a common section that often leads to fire spreading to nearby buildings). It is non-combustible and heat-resistant to temperatures over 530 Celsius (1,000 Fahrenheit) for up to three hours. When seconds and minutes make all the difference, assurances comes from a material’s ability to resist higher temperatures before critical failure. Adding in fire barriers and thermal breaks between sections within the building adds in further fire preventive measures.
Buying critical time – time to escape the building, time to allow fire departments to arrive – is the difference between safety and catastrophe. Buildings become safer by providing more time for people to clear. These measures (steel materials, fire-rated glass, fire barriers) also provide protection for the building, limiting the spread of flames, smoke and toxic gases and decreasing the amount of damage caused. Although safety protocols may reduce the risk of fire, the risk will remain, especially in industrial settings. The best risk-management strategy is to reduce the risk and get back to operations as soon as possible if one does occur.
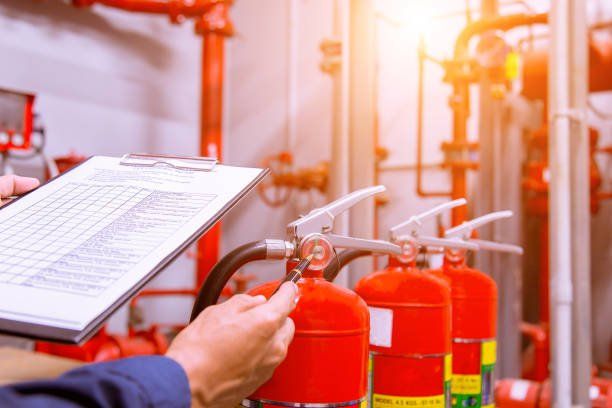
Fire-resistant materials do not affect design
Architects and engineers incorporate steel and glazed glass throughout the structure according to local building codes all the way to the top of the structure, whether it be a one- or two-story steel building. Exterior walls, and using pre-engineered steel panels with special fire-resistant insulation, reduce the spread of flames and radiant heat from one building to any adjacent ones. All these features are built seamlessly into the structure. Glass and cold-form steel are attractive and can be finished in many ways to fit in with whatever aesthetic design you want.
Read how building with pre-engineered metal systems can protect you from wildfires.
Steel limits the extent of damage in the event of fire
In the event of a building fire, it’s natural to look at the extent of the damages and the overall cost to replace and repair. Steel buildings emphasize the benefits and costs of fire prevention in advance to eliminate potential incidents in the first place. These preventative measures place less burden on buildings owners and help reduce replacement costs. If an incident does incur, lowering the extent of damage also helps reduce the costs of any subsequent insurance and legal claims, both to the immediate structure, and also to any surrounding businesses and property.
With all areas (such as loading docks, stairwells, operational and administrative areas) being divided by thermal barriers and spacious fire/thermal breaks, it is easier to emergency personnel to quickly limit the spread and extent of the damaged to the structure. And because of pre-engineering’s design, replacing sections of a steel building is easier and less costly than with other materials, such as brick and mortar or mass timber.
Summit Steel Buildings incorporates fire resistance into every building’s design from the initial concept as they do with all the other environment and utility systems. A proper safety plan that includes sprinklers, emergency exits, and sensors and alarms ensures your building is ready for operation at the best of times with preparedness for the worst. Non-combustible cold-formed steel buildings, pre-engineered metal components and fire-protective glazed glass work together to become a shield against the dangers of fire, while minimizing the extent of costly damages if anything should happen.
Rely on Summit Steel Buildings’ engineering to prevent fire and damage
Matches are made from wood for good reason. Steel and glazed glass are better materials to prevent and reduce the incidence of fire. Building with steel is more modern, sophisticated, faster and less expensive than traditional building systems but also create a safer working environment. Using steel construction becomes the smarter way to protect people, materials and the building itself (yours and your neighbours) and to prevent, contain and limit resulting damages from accidental fires.
To learn more about how pre-engineered steel buildings can protect your commercial or industrial business,
contact our team at Summit Steel Buildings to get your free quote and preliminary drawings.
About the author
Frank Melo has a construction civil engineering technology and business background with over 25 years of experience as a business owner and contractor. He was born and educated in London, Ontario and now divides his time between projects primarily in Ontario and British Columbia. He can be contacted at Summit Steel Buildings at (778) 951-4766 or by email at frank.melo@summitsteelbuildings.com or through LinkedIn.